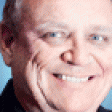
While it may appear that a diverse manufacturing business limits the urgency and opportunities for automation, the inverse is probably true: the age of continuous change and rapid go-to-market times dictates that manufacturing companies need to be agile in what they make and when.
Production runs need to be diverse and ever-changing - in short, more than ever before, manufacturing businesses need to be agile.
Manufacturing capacity in SA is being under-utilised. According to StatsSAas of February 2013 "utilisation of production capacity" is only 79%.
Within the context of manufacturing, where production is customer-driven and where there is a need for diverse production runs - and where these runs are relatively short, the level of utilisation of production can be improved by production agility.
The ability to be agile with production runs depends on three things: set-up times, bottlenecks and size of stock piles.
If set-up times can be reduced, production runs can be changed as often as needed; if there is a lean production environment, stock on the production floor (getting in the way and costing money) can be reduced; and if bottlenecks (which will shift) are clearly identified and understood, then companies will feel comfortable to change runs fast.
Keep it lean
Lean manufacturing is a manufacturing philosophy that addresses these three problems (as well as other areas).
The guiding principles of lean manufacturing are 'eliminate waste' and 'respect for people'.
Eliminate waste:
Toyota's president, Fujio Cho, defines waste as "anything other than the minimum amount of equipment, materials, parts, and workers (working time) which are absolutely essential to production".
Seven areas where waste can be eliminated are:
1) Small specialised plants - small plants lend themselves to flexibility and can be designed to be more economical by specialising in specific areas. With the right planning and automation, they can rapidly swap runs.
2) Grouping - the grouping of all the machines and tools around the operator rather than having the goods moving to different shops reduces movement and queues between workshops. This requires multi-skilled operators, but provides more variety and therefore greater worker satisfaction.
3) Quality at source - having smaller sub-processes means production quality can be inspected by anyone at any point in the process, and not just at the end. If component quality is perceived to be slipping, it can be fixed immediately, thus avoiding knock-on effects. Use automatic inspection wherever possible - record everything and reflect on the process with statistics in hand.
4) Just-in-time - this controls the movement through the production process based on a pull from the sales orders. It addresses time and stock waste, identifies bottlenecks and continuous improvement - but it also requires employee participation. According to engineering theory, a lot size of one is ideal, but this is impractical and not cost-efficient. In practice, a multi-disciplinary team needs to look at engineering issues, markets, transport, set-up costs, etc, to decide on the most cost-effective lot size. Continuous improvement is achieved by addressing backlogs (inspection, paperwork, order entry and decision), work in progress queues, design redundancies, change orders, scrap, returns and machine downtimes.
5) Uniform plant loading - production must flow as smoothly as possible in order to dampen the effects of changes in the flow. This is not about the disruption during the changeover, but is the local optimisation and design of every specific run and the careful planning of what must be produced and where in the plant.
6) Kanban production control systems - this was discussed in my previous Industry Insight.
7) Minimised set-up times - the speed of changing to a new production run. This involves training and practice of staff, clever design of each production, swap-over and set-up process, and the use of automated machine set-up equipment like MES (manufacturing execution systems) that monitor the equipment and actually automatically control the set-up of machines.
Respect for people
Giving respect to people is a complex matter, but is critical to the success of an agile production business.
One will not be able implement lean manufacturing successfully without the buy-in of the people. People will need to be challenged, motivated and proud of their agility and production quality. Most important of all is that they need to see what they personally gain from the process - and this needs to be positive motivator.
The overall motivation needs to be multifaceted and include remuneration, incentives, corporate culture, physical working conditions, etc. Here the value of ERP systems like Dynamics AX, which implements the lean manufacturing process, are ideal for running the human resource side of a manufacturing business as well.
Automation is not only a useful production environment that is diverse and has frequent changes in runs; it is the key to agility. At the same time, automation can reduce human error and cut the set-up times and management of rescheduling and ordering of stock.
Effective ERP can also ensure the human resource processes are managed and staff members are well informed of changes to processes, policies and business successes. Automation can greatly enhance agility.
Share