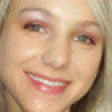
With names like yttrium, gadolinium, and neodymium, rare earth elements aren't exactly the celebrities of the Periodic Table. Most people have never even heard of them. But without these oddly-named metals, we wouldn't have efficient light bulbs, ultra-thin TVs, super-fast computers or renewable energy applications.
Rare earth metals have been making headlines lately due to concerns that shortages of these elements could spell disaster for the green tech and consumer electronics industries.
The 17 rare earth elements are vital components of a variety of technologies, including cellphones, computing devices, TVs, lasers, solar cells, electric car batteries, wind turbines, and advanced weapon systems. The role they play often seems minor or niche, but without them, many products would be useless or considerably impaired.
Imagine still watching TV in black and white, for example (europium provided the red phosphors that paved the way for colour TV sets), or struggling with slow connections (erbium speeds up optical-fibre networks), or bothering with old-school light bulbs (thank neodymium for compact fluorescents).
While they aren't really rare in terms of being scarce, rare earth elements are difficult to find in concentrations high enough to make them economically viable to extract. Only a few countries in the world are involved in the production of these metals, and even after discovering a potential site, it can take up to 10 years before a company is able to even begin rare earth mining. The mining of these metals can also be environmentally damaging, as extraction produces millions of tonnes of waste water containing harmful chemicals and radioactive by-products.
This was never really a problem until about 20 years ago, when the sudden explosion of technology meant rare earth metals' use in miniaturised computing systems, computer memory, rechargeable batteries, cellphones, cameras, communication networks and other applications made them a hot commodity.
Chinese production started to increase dramatically, causing falling prices worldwide.
Dr Vogt, CSIR
Rare earth materials are used in several processes in semiconductor manufacturing, and with mobile devices such as smartphones and tablets being churned out at record rates, these metals are only likely to become more sought-after in future.
The rise of 'green' technologies like wind turbines, solar cells and electric vehicle batteries is also pushing demand, with clean energy technologies making up around 20% of the global consumption of critical rare earth metals. Commenting in his personal capacity, Dr Declan Vogt, manager of the Centre for Mining Innovation at the CSIR, notes that as the world moves towards low-carbon technologies, demand for elements will climb further.
“Magnets made using rare earths are stronger, so they can be used to make motors that are smaller and lighter. These motors and generators are important in green technologies, as cars go to electric and as more electricity is generated from wind.”
Some large wind turbines, for example, can use up to two tonnes of these magnets. This increasing demand, coupled with the limited number of rare earth sources, is causing something of a scramble among governments and industries, as they try to find ways of addressing possible shortages.
Under pressure
The US Department of Energy (DOE) has identified five of the 17 rare earth elements as particularly significant in its recent critical materials strategy, in terms of their importance to clean energy technology and risk of supply disruption.
They includeyttrium - a key element in phosphors for CFLs, TVs and LCD screens - for which there is currently no known effective substitute. Demand for yttrium could rise even higher, says the DOE, “if high-temperature superconductors begin to capture market share from permanent magnets used in other applications such as wind turbines”.
Dysprosium is another metal on the critical list, as it's crucial for magnets capable of high-temperature operations (particularly in vehicle drives).” With the push to promote electric cars, demand for dysprosium is likely to keep going up. And, for now, the only known substitute is the even more rare and more expensive terbium,” states the report.
Terbium obviously also makes it onto the list, and is used as a phosphor in fluorescent lighting. Ongoing advances in LEDs could eliminate the need for terbium in such cases, but not until at least the medium-term, says the DOE.
Europium is also used in phosphor compounds for CFLs, and with the use of these light bulbs increasing as Europe and the US phase out incandescent bulbs, demand for the element is expected to keep rising. There are no proven substitutes that work in CFLs, according to the DOE assessment.
Rounding out the top-five list is neodymium, used mostly in the clean tech sector to produce high-strength magnets for electric cars and wind turbines. According to rare earth miner Lynas, in 2010 there was a demand for almost 30 000 tonnes of neodymium and a supply of only 22 729 tonnes. For 2014, the predicted demand is over 45 000 tonnes, with a likely supply of under 32 000 tonnes.
As new mines come on stream, prices will drop to pre-crisis levels and lower.
Dr Vogt, CSIR
Vogt mentions that some companies are making provision for potential shortfalls. “Hitachi has developed a new motor that works efficiently without rare earths. Other major manufacturers including Toyota are working towards the same goal.”
He believes the biggest challenge facing rare earth metal production is processing them efficiently, while extracting them from their host rocks. “Toxic acid is used in their processing, and can lead to environmental problems if not handled correctly.”
Dr Leon Kr"uger, manager of the hydrometallurgy division at Mintek, says while rare earth minerals are not actually rare at all, the complexity of mining them poses major challenges. “Because of their geochemical properties, they are typically dispersed and not often found in concentrated and economically exploitable deposits. Coupled to this is the complex mineralogy and low grade of these deposits. It would require innovative and flexible technology to extract the valuable rare earth elements and concentrate them up to the point at which they can be refined cost-effectively.”
He adds that since many deposits would have to be processed together to operate at a scale that's competitive in a global environment, the scheduling and integration of different production plans is expected to be a major risk to the provision of a stable supply to a refinery.
“It is therefore important to provide the appropriate technology, ensure stable feed to a refinery and secure stable off-take of the products from the refinery,” says Kr"uger.
The DOE adds that over the past year, prices of many rare earth elements have been highly volatile, in some cases increasing ten-fold. The main reason for this is the fact that a single country is responsible for more than 95% of the world's rare earth production.
Metal monopoly
While there were rare earth mines in many parts of the world, including India, Brazil, SA and the US, things changed significantly in the late 1980s and early 1990s, notes Vogt. “Chinese production started to increase dramatically, causing falling prices worldwide, which closed most non-Chinese mines.”
China's cheap labour, lax environmental standards and government support allowed it to sell rare earths at such low prices that previously prominent sites like California's Mountain Pass were unable to compete.
“In 2009, China announced that it would reduce its export quota of rare earths, causing something of a panic,” adds Vogt. “In the medium-term, many countries are re-opening existing rare earth mines, but in the short-term, there might be shortages.”
Kr"uger points out that China has several world-class rare earth deposits, with the one at Bayan Obo being the largest in the world. He adds that much less consideration and expenditure is given to environmental concerns and waste treatment than in a typical Western operation. “This means that Chinese production costs are much lower than anywhere else and they have used this advantage very effectively in the past few decades to suppress rare earth projects or developments outside of China.”
The recently imposed limits on exports to control prices led the US, the European Union and Japan to file a complaint with the World Trade Organisation in March. China has since relaxed its quotas, but concerns remain about the country's monopoly. The Chinese government estimates that at the current pace of mining, China will run out of all heavy rare earth elements in approximately 15 years.
The accessible reserves of elements like neodymium (hard disk drives, electric cars, wind turbines) and indium (LCDs, touch-screens, solar cells) are only predicted to last another 10 to 20 years, and some scenarios suggest shortages could extend to 2016 if demand is high and production doesn't ramp up. By 2015, the world's industries are forecast to consume an estimated 185 000 tons of rare earths, 50% more than the total for 2010.
As a result of the increased demand and China's restrictions on exports, some countries have begun re-opening their existing rare earth mines. The US' Mountain Pass mine, for example, is back in operation after closing down in 2002 (due to environmental hazards) and plans to produce 40 000 tonnes annually by the end of 2013. Prospecting is also being done for alternative rare earth sources in Australia, Brazil, Canada, India, SA, Tanzania, and Greenland.
“China has in the past, and is likely to do so in future, manipulated supply to discourage new developments,” says Kruger. “These manipulations are likely to have short-term influence on the price of rare earth elements, but due to projected shortages of certain (mostly the heavier elements) even when new supplies such as Mountain Pass and Lynas come on stream, the long-term price development of rare earth metals is likely to remain good.”
Vogt believes China's quotas are unlikely to have lasting impacts. “It'll cause a short-term price increase while supply is short, but new mines will come on stream and prices will drop to pre-crisis levels and lower.”
Mining junk
One way of mitigating potential shortages is recovering rare earth metals from discarded electronic equipment. This kills two birds with one stone, as it also leads to the processing of electronic waste that is currently clogging up landfills, causing heavy metals and toxic wastes to seep into nearby soil and water supplies.
While rare earth elements are not being recycled in large quantities yet, a recent report by the US Geological Survey says in the event of shortages, prices could increase to the point of making recycling activities feasible. “There are ongoing research activities into reclaiming rare earth elements from the scrap generated in the various end-use sectors,” states the report.
Advances in recycling technology are making the recovery of rare earth elements from used equipment more feasible, and recycling plants are now operating in places like Japan, where an estimated 300 000 tons of rare earths are stored in unused electronics.
Japanese companies are also joining in. Hitachi, for example, has begun recovering neodymium and dysprosium from magnets in its hard drives and air conditioners. Toyota and Panasonic, meanwhile, are working together to recover components from the Prius hybrid cars to reuse in consumer electronics.
Another innovation was recently announced by Honda and Japan Metals & Chemicals, in what they say is the first mass-production process for recycling rare earth materials. The companies are applying the process to hybrid vehicle batteries and scrap metal from cars. According to a Honda statement, the process enables the extraction of over 80% of rare earth metals contained in used nickel-metal hydride batteries. The automaker says it aims to reuse the metals in a range of products, and if the process is successful, it could potentially have implications for other industries.
It remains to be seen whether recycling initiatives and new mines will be enough to satisfy the growing appetite for rare earth elements in future. Either way, these metals are quickly shrugging off their mantle of public obscurity, and look set to move from chemical unknowns to the Periodic Table's most talked-about characters.
Share