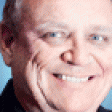
This Industry Insight is focused on addressing the value of lean thinking in manufacturing. In a previous Industry Insight, attention was given to the two key principles of lean manufacturing, namely the elimination of waste and respect for people.
The Japanese use the word muda (waste) as something in the process that does not directly add value to the customer. They also follow two other concepts - mura (inconsistency or irregularity) and muri (literally overburden), which produces stress on the production resources, including people.
Mura relates to stop-start processes and non-compliance with standards that result in inconsistent products (and therefore the need to have to re-do a job or change a later process to accommodate a non-standard component), thus disrupting the flow of operations.
Muri refers to a scenario in which some people and machines are idle, while others overwork. This leads to machinery break-downs and people who are either sick or so exhausted they make mistakes.
Time out
It is also about respecting people in the sense that one should never have people working at 100% capacity every minute of every working day - they need spaces (even if small) to re-gather themselves and also to think about improving what they are doing.
Lean thinking has led to a re-evaluation of how production can be more effective, and amazingly has come to the realisation that the end-client is actually important. To some extent, the industrial machine, created to fuel the industrial revolution, ended up focusing on local efficiencies and lost sight of the needs of the client.
In order to derive the cost benefits of mass production and large batches, everything has been componentised as far as possible and the principles of muda, mura and muri applied as far as possible.
Mass production requires large machines, which require large capital outlays, and since large volume production is only viable in very big and widespread markets, centralisation was the next logical step. Sadly, in this environment, workers often become no more than machines doing mind-numbing, repeatable processes day-after-day to produce these "standard components".
Speculation
Great cost benefits have been derived from this approach at the component level of this process, and this remains a valid paradigm. However, all is not as it could be and there are significant problems of guessing (I call it estimating) requirements. Since the customer expects timely response on orders for these goods, the only way to manage this is stockpiling and either doing so wherever the item is sold or providing efficient transportation.
So items produced en-masse in Japan are stockpiled and await shipping, then stockpiled at central depots in this country, then stockpiled in towns and maybe even at several places in the city. The store-and-forward mechanism ties up huge amounts of working capital, often for very long periods of time. If the estimates for original production are wrong, then the goods ultimately get scrapped.
The ideal is a batch of one when asked for.
All of this is built into the consumer pricing and could conceivably negate the savings of mass production. Enter lean thinking, which says companies should only produce what the customer needs when it is needed. Underlying this is the engineering estimate that the ideal batch is one, since this reduces waste and tied-up working capital. I will expand on this in the final Industry Insight in this series.
Plugging the drains
So, what are the seven drains on working capital in a manufacturing environment - those that lean thinking can address? Cash-flow problems can be improved, as well as tied-up working capital, if the following can be eliminated or reduced:
* Wasted time. Time means money, so there needs to be a reduction or removal of all time spent along the entire chain from actual demand to customer payment. This relates to local efficiencies at component manufacture stage, assembly time, storage times along the entire chain, transportation time, and time on retailer shelves. The ideal is no waiting time in the whole value chain.
* Re-doing work or repairing what was not done right. The ideal would be perfect goods all the time.
* Producing what is not yet needed or more than is needed. US statistics reveal 40% of all books produced for the US market get shredded. This results in a vicious cycle of higher cost to client to cover this, and therefore, fewer sales, which leads to more waste if production is not aligned. The ideal would be a batch of one when needed.
* Stockpiling. Having to hold stock against projected sales in order to meet customer response times. In the case of mass-produced goods, this is a direct result of long value chains and huge batches which result in very long lead times from production to delivery. The 'ideal' would be manufacturing to requirement and delivery from a local manufacturer directly to the customer.
* Running equipment when it does not need to run. This is a natural outflow of mass production - a machine produces huge numbers of an item that is never sold. This is unnecessary wear on machinery. The ideal would be only to run the machine if there is a customer waiting for this item. Again, the ideal is a batch of one when asked for.
* Money wasted on unnecessary transport. This covers everything from in-house between machines, between factories, between countries and between depots. This translates to money tied up in equipment such as conveyor belts, forklifts, shipping containers, etc, as well as being tied up in stocks waiting for a large enough batch to warrant transporting (ie, a truck or container load).
* Staff issues and strikes that leave plants standing idle. The ideal would be to have happy, motivated staff. Unfortunately, mass production is to a large extent dehumanising and relies on production statistics (stick) and salary (carrot) to motivate people. The ideal would be to have everyone involved in end-to-end production and having them handle and evaluate the final product.
Leading manufacturers are starting to hear the call to move to lean thinking and are starting to effectively apply IT to implementing this approach.
They are using:
* Customer relationship management software to bring the user closer to the production environment, by capturing user requirements and being able to feed this in near real-time to the retailers and manufacturers. This is enabling the principle of "pull".
* Enterprise resource planning systems, such as Microsoft Dynamics AX, which have modules specifically designed to support lean manufacturing. These provide powerful tools for identifying where time is being wasted and for assisting to significantly reducing overall stock and stock aging. It also helps in driving down errors.
* Workflow and tasking (which may also include scheduling). This can be used to manage the whole "pull" process as well as potentially providing the visibility of the process and goods within that process. It can also be used to enforce the use of correct processes and methodologies.
* Collaboration environments and planning, such as that provided by Microsoft SharePoint, which can allow entities along the entire chain to work as a single unit to more effectively meet customer demands.
From quote to shipment: quickly and profitable every time. Discover the truth about IT solutions of the manufacturing business!
Share