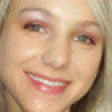
With its cartoony wheels, plume of wires, and compact circuitry, the charming little robot trundles across the tile floor, its infrared sensors peeping out like crab eyestalks, watching for obstacles. When nearing a corner, it starts to turn somewhat awkwardly to try and avoid a collision, furiously wheeling back and forth with a mechanical squeal. The miniature battle for mobility seems positively valiant in its earnestness.
The roaming bot, called Skippy Robot, can easily be assembled from Meccano strips, a few nuts and bolts and a motherboard, making for a nifty DIY project. Its struggle to navigate its surroundings, however, also reveals the highly complex nature of an activity most animals do without a second thought. It's this evolved ability to adapt motion to one's circumstances that researchers are working hard to recreate in robots, as a new class of human assistants is forged.
To enable a machine to walk like a human requires an enormous amount of programming and engineering to respond to the multi-sensory information we process in the blink of an eye. And humans aren't even the ideal models for effective motion. The movements of insects and reptiles are far more promising as inspirations for the robotic creations set to become our future soldiers, caretakers and rescuers.
Researchers are looking to the animal kingdom for ideas, to capitalise on their strengths without involving living beings, or even to improve on nature's designs.
One team at the Sant'Anna School of Advanced Studies in Italy, for example, is trying to build a robotic octopus. As detailed in The Economist, researchers hope to reconstruct the sea creature's powerful, pliable arms to perform tasks that call for both strength and dexterity.
Because it lacks the skeletal support of its vertebrate peers, an octopus has arm muscles that must both move and carry the weight of the arm. This allows it to access hard-to-reach spots while getting and maintaining a firm hold on whatever it needs to (one possible application is going underwater to shut off leaking oil valves).
Even the robots at the bleeding edge are still relatively clunky.
Andre Hoffmann, Broadband Infraco
At Stanford University in the US, another team of scientists has built a robot that mimics the climbing ability of geckos, based on their use of directional adhesion to scurry up vertical surfaces. The latest version, Stickybot III, is capable of scaling a wall at 5cm per second, not a patch on real gecko speeds of nearly a metre per second.
Many of these projects fall into the fields of biomimetics (imitating natural systems in the design of materials and machines) and bio-mechatronics - the integration of mechanical, electronic and computer engineering with biology.
Johannes de Vries, from the French South African Institute of Technology at TUT, notes that engineering is all about solving problems. “Studying nature's solution to problems creates new opportunities for engineering solutions. Nature can inspire new ideas. One idea leads to another, bringing improvements to existing designs and eventually some kind of solution.”
He adds, however, that taking cues from the natural world isn't always a straight-forward exercise.
Loco-motion
Firstly, nature has a bit of a head start on the design process.
Riaan Stopforth, who heads up the search and rescue division and bio-engineering unit within the Mechatronics and Robotics Research Group at the University of KwaZulu-Natal (UKZN), says evolution has allowed natural systems to benefit from millennia of trial and error.
“Nature has been designed and developed at its optimal manner, and as engineers this is a true benchmark to compare our robotic systems with.”
With this in mind, researchers are increasingly looking to insects for design inspiration, because when it comes to efficient heavy-lifters, creepy crawlies are nature's top achievers.
A key feature is the ability to modify behaviour according to circumstances, notes Stopforth. “Consider an insect; if it loses a leg, it is able to adapt to this situation and continue walking with the other legs.
“Another example is a cockroach. This insect has the amazing ability to continue walking, and possibly live, even if it's been partially squashed. Similarly, these roaches are able to manipulate their bodies to squeeze under doors and so on.”
Most people observe these capabilities, if at all, with annoyance, as they chase a seemingly invincible critter around the kitchen. But this never-say-die quality proves valuable in robotics, notes Stopforth.
Take search and rescue robots, for example, which often function in harsh environments where building materials could fall on them and disable a particular feature. If the robot can adapt to the accident and use its other features to continue with the search, it's hugely beneficial, he explains.
Jeremy Green, a senior researcher at the CSIR's Centre for Mining Innovation, notes that while the natural world has developed highly versatile, effective processes, they also involve a great degree of complexity.
For this reason, nature is often used as an inspiration for system design, rather than a template that is copied, he says.
“In nature so many things work harmoniously together to get a system to function. Mimicking them usually involves understanding many fields - from biology, chemistry and physics in understanding what is actually happening in nature, to mechanics, mechanical, electrical, computer and software capabilities in creating a system that can mimic nature,” says Green.
Another difficulty is the algorithms and artificial intelligence (AI) needed to translate the motion, says Stopforth. “Replicating a mechanical structure for an entity is not too difficult with the current technologies, but having this entity move in a certain way becomes challenging.”
Robots always need to have power and every source has it limitations.
Johannes de Vries, TUT
Animals also have the advantage of a biological structure that is more flexible and involved. “If you consider an insect, or even a human, there are so many muscles and joints that allow for certain tasks to be performed that it becomes very difficult to replicate them in a robotic system.
“We are able to replicate the biological systems into a mechatronics fashion, but it is difficult to achieve the same efficiency, torque and strength in the same space and structure, especially when cost is a major factor,” adds Stopforth.
Finding the force
To achieve this complex motion, there needs to be some kind of decision-making process, says De Vries. “Mechanical and electrical systems need to work together. Some feedback needs to be incorporated, be it the position of a motor, arm, leg, the robot itself, or the orientation of the robot.”
Andr'e Hoffmann, a founding member of the Robotics Association of SA and chief engineer of transmission engineering at Broadband Infraco, says the problem needs to be tackled at various levels. This includes everything from writing software programs for simple movements, to finding lighter materials. “Every year the technology gets more sophisticated, but we still make a lot of mistakes. Even the robots at the bleeding edge are still relatively clunky.”
Hoffmann believes a convergence in the fields of biometrics and traditional mechanical, electrical and computational systems will trigger a major revolution in the capabilities of robots.
Even if robots manage to master fluid movements, there's also the energy component to consider. “One of the biggest challenges is power. Robots always need to have power and every source has it limitations. Batteries, for example, are heavy and need to be recharged, while fuel systems are noisy and more difficult to control,” says De Vries.
Professor Glen Bright, who heads up Mechatronics and Robotics Research Group at UKZN, says it comes down to the energy required to move a mass. Bulky metal bot parts need a lot more oomph to get going than the feather-light limbs of an insect.
To solve this problem, says Bright, parallel kinematic manipulators are used to reduce the overall mass. Instead of having a solid link between the robot and its moving joints, several smaller rods are used, making for lighter parts.
Researchers can learn a lot from the insect world in terms of efficiency and energy conversion, notes Bright. “An industrial robot used to put a car together, for example, typically weighs half a ton with a payload of about 35kg. An ant weighs one gram but can carry 10 grams. It's more efficiency using less energy.”
Robotscience founder Michael Ettershank adds that the ultimate progression of robotic designs inspired by nature tend be more human-like. “But these require pretty expensive electronic accelerometers, gyrometers and rotational force sensors in order to balance and not simply tumble over into a heap.
“The advantage of copying spiders with eight legs and insects with six legs on the ground is they're pretty stable and can walk over rough terrain and step over obstacles if they have enough ground clearance.”
Getting multiple legs to work in unison is no easy feat, however, which is why Stephen Marais, of the Robotics and Agents Research Lab at UCT, is trying to teach a robot how to walk. The aim is to get the six-legged, insect-like robot to figure out how to walk by itself, though reinforcement learning (when its body is on the ground, it's bad; if it's upright, it's good).
“We're doing a lot of work on the hardware side so the robot is tough enough, because it falls down a lot and breaks itself into pieces.” This research could eventually result in robots that have the ability to adapt, so if they break a leg while in the field, they can re-teach themselves to walk - much like those cockroaches which manage to scurry away half-squashed.
Rescue rangers
Another one of the UCT lab's projects is to build an urban search and rescue robot, which would investigate destroyed or damaged buildings to search for survivors and assess whether it's safe for rescue teams to enter.
Bright says events like 9/11, the Haiti earthquake and the mine disaster in Chile have significantly raised the profile of search and rescue robots.
“Fire-fighters are able to use robots to locate victims in dense smoke areas,” notes Stopforth. “The advantage of using robotic systems is that if danger should occur in these environments, such as an explosion or a burning building collapsing, no human or animal rescuers are harmed.”
Robots are also being used to survey dangerous zones, with the military using them to scout areas or detect dangerous substances, he adds.
One of the companies making huge strides in this field is Boston Dynamics. Its Big Dog creation is being prepared for war by a company responsible for carrying US military troops in and out of danger. The impressive robot can jump into the air, run up slopes covered in loose rocks, and navigate rubble while carrying up to 150kg.
Marais says the problem facing every robot system at the moment is simultaneous localisation and mapping (Slam), which enables robots to find their position in an unknown environment. It allows them answer the question 'where am I in the world, and what does it look like?'
This is a crucial requirement for robots to make decisions in situations they haven't encountered before, says Marais.
All these factors depend on what Bright sees as a key development - the integration of robots' various systems. “Advances are being made in the separate fields of hardware, software and AI, but it's all about the integration. Software and electronic systems have been well developed, due to their commercial applications, but mechanical systems are lagging behind, he says.
Despite the numerous challenges, Marais believes there are major opportunities for breakthroughs ahead.
“If someone comes up with a radical new way to achieve linear motion, they'll be the winner in this race. Developments are happening increasingly rapidly, so watch this space.”
* Look out for part two of this feature series next week.
If you liked this story, you might also like: Rethinking machine intelligence,Sci-fi meets society, AI comes of age
Videos:
Something fishy
Boston Dynamics' 'Big Dog'
Boston Dynamics' Little Dog
Share