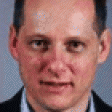
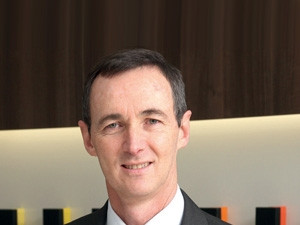
In the face of volatile commodities prices, climbing labour and power costs, and growing regulatory scrutiny, South African mines are taking the knife to their operating expenditure. In addition to paring headcount, many mines are looking to trim discretionary spending on IT as part of their cost reduction strategies.
But at the same time, mining operations are being forced to use technology in a far more strategic manner than they have in the past. "The oil and gas sector uses technology with finesse, where the mining industry has always used it with brute force," says AccTech sales director Marc Gower. That picture is changing as mining companies start to embrace technologies such as big data to improve management of their resources.
The never-ending need to control costs to extract ore in the most profitable manner is the key factor driving adoption of technology in the mining sector, says Jeremy Waterman, MD of Sage ERP Africa and Middle East. Once the basics of a robust multilingual, multi-currency and multi-legislation ERP system are in place, the next challenge is using transactional data to improve decision-making, he adds.
One advance in this regard is use of mobile technology to deliver meaningful reports to staff in the field. Supervisors, middle managers, and senior leadership are increasingly able to view data from multiple sources, including financials, geological, production, EAM, HR, payroll and time and attendance systems on their PCs or tablets as part of a single intelligence platform.
Slash and burn
With the industry in crisis, most miners don't have the time to give careful consideration to their investments in IT, says Duncan Sloan, industry lead for chemicals and natural resources, Accenture SA. "The slash and burn mentality is the first reaction," he adds, as companies seek to boost operating efficiencies in the first phase of a crisis.
But as the crisis unfolds, miners will need to adopt digital technologies to ensure their much reduced workforces in the mines and offices can keep working efficiently, says Sloan. In addition to optimising human resource management, they also need to ensure they are maximising their investments in fixed equipment and other assets.
"Mines are no longer running machines to failure," agrees Gower. They're connecting equipment to the IP network and using analytics tools for conditional monitoring and maintenance, and for life cycle costing. These machines create big data that miners can turn into intelligence they can use to enhance decision-making.
The oil and gas sector uses technology with finesse, where the mining industry has always used it with brute force.
The hi-tech mine of tomorrow will use embedded sensors, analytics, cloud solutions, social media and mobility to ensure operational efficiency, says Sloan. CIOs will need to get their hands dirty in operations to help their companies make better use of their investments in process control and field devices.
He sketches a picture of a mining operation where fixed equipment, such as the primary crusher, has embedded intelligent sensors connected to a ubiquitous network. If the crusher experiences an out of tolerance condition, an engineer is dispatched to repair it. Completed work orders are analysed in memory by an analytics engine.
Based on historical data about crusher performance, as well as access to the OEM database in the cloud, specific failure trends can be identified. This enables management to take action to avoid similar equipment failures in the future.
A common language
One of the major trends that specialist IT vendors say they're seeing unfold in the mining sector is a shift towards tighter management of application costs.
Craig Peek, customer services manager for Africa at Micromine, says his company is seeing a strong trend towards software consolidation in the South African mining industry. Most miners are looking for 'one throat to choke' as they rationalise their software platforms to improve efficiencies.
Against this backdrop, the approval of a reference model for IT in natural resources earlier this year could help mining companies save money on managing their application portfolios. Local mining groups are set to benefit from the approval of the Exploration and Mining Business Reference Model (EM Model) as an Open Group technical standard.
This model is the first step towards establishing a blueprint for organisations in the natural resources industry, with the goal of providing standard operating practices for vendors that offer technical and business solutions to the industry.
Once organisations know precisely what is in their portfolio, they can save millions a year.
The Exploration, Mining, Metals and Minerals Forum is a forum of The Open Group, with members such as MineRP, Rio Tinto, Lonmin Platinum, CAE Mining and Fortescue Metals Group. The standard delivers a reference model that stands up to scrutiny in multiple mining environments, says Stuart Macgregor, CEO of South African Open Group representative, Real IRM.
For suppliers and vendors, the benefit of the EM Model is as a sales tool. It allows them to find partners, align themselves with customers' architectures, and help drive industry standards, says Macgregor. Vendors can use the EM Model to engage with any mining operation and any mining method, since it captures the mining business generically.
By using this model to shape software development, vendors can create a framework for enterprise integration that transcends the information flow boundaries once introduced by different mining types, geologies and multiple disciplines, Macgregor adds.
For mining companies, cost-efficiencies are at the top of the list of the potential benefits of the EM Model. They will be able to use the model for application portfolio rationalisation and to improve their selection and procurement processes, says Macgregor. They'll also be talking to suppliers using business terminology with common definitions. "Once organisations know precisely what is in their portfolio, they can save millions a year," he adds.
Share