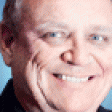
The production process is complex but fascinating. The process runs all the way from marketing, quotations and orders, through ordering and acquisition of materials and components, on to the actual production and shipping of the final product. This holistic process may make use of customer relationship management (CRM), manufacturing execution systems(MES) and enterprise resource planning (ERP) software, which all contribute to implementing and controlling this production flow.
The concept of "economy of scale" led to mass production, which in turn led to what most manufacturers see as the "normal" design for production lines. This is still a valid approach for some instances of the actual manufacturing. It is, however, not ideal when seen in the context of the end-to-end cycle, as it introduced the need for huge stockpiles running all the way from the centralised mass-production facilities to the consumer outlets.
The key to optimised production, which minimises or even eliminates waste in terms of materials and time (and therefore maximises profitability), is to be found in the design of this production "system". This is where the Japanese car manufacturers introduced the concepts of first "in-time" and now "lean" manufacturing, to try and deal with the stockpiling and bottlenecks that occur from unsynchronised, mass, component manufacture.
Just-in-time thinking led to the introduction of kanbans (initially as physical cards that move around the factory) for getting the production line to flow more effectively, by pulling materials and components only when needed. Lean manufacturing grew out of the need to eliminate waste. ERP systems came into play to plan production and re-ordering based on sales forecasts and lead times, but this did not address the elimination of waste and flow problems.
Big in Japan
As noted earlier, the holistic system is complex, and so the way it is designed is paramount in achieving success. The extent and nature of MES's control, the flow of jobs, the use of pull or just-in-time, essential stock levels, set-up times and integration and automation of ERP all need to come under consideration. Getting this right is "big in Japan", and should be the same here in SA if businesses want to compete in the global arena.
To cater for the manufacturing industry, Microsoft Dynamics AX brought in the Manufacturing Resource Planning (MRP II) engine to try and fill the most important gaps and to integrate the elements of the holistic process. MRP II functionality works with the lean manufacturing functionality, providing the capability to design a production system that caters for just-in-time elements as well as long lead time, make-to-stock components of a business.
Lean manufacturing was designed using the concepts discussed in my earlier Industry Insights - that is customer value, value stream, flow, pull, and perfection, as formulated by Womack and Jones in their book Lean thinking (Womack, James P; Daniel T Jones. Lean Thinking. Free Press, 2003)
Costing of the production, and updating the inventory balances, is tricky with manual and most computerised systems - should the company back-flush, should it use picking slips for everything, should it monitor work-in-progress (WIP)?
Costing quandary
To address this costing dilemma, Microsoft Dynamics AX 2012 introduced activity-based production flows as the backbone of lean manufacturing. This means the costing is independent of the bill of materials line quantities and scrap factors; consumption can be reported more accurately without having to report quantities by job.
Lean manufacturing grew out of the need to eliminate waste.
To start seeing the utility of this software, look at an example of one scenario using AX (obviously, the ERP system will allow the company to configure an infinite number of different designs for its business):
The CRM system is keeping control of a company's walk with its customers, thereby providing early warning of any potential orders. AX manages these prospects, leads, opportunities and contacts, through telemarketing and campaign management. While doing this, the data in the system is being used to predict sales forecasts, which are used by the master planner (AX's MRP II engine) to schedule the ordering of components that are not supplied on a just-in-time, pull basis.
Once a sales order is confirmed, a kanban is created for this order and this initiates the whole pull chain - the flow begins. Picking orders for replenishment stock - those not controlled by kanbans - are created based on stock levels and time fences in order to keep optimum stock levels for the kanban pull to access.
Electronic kanban boards display each job (in different colours, representing different configurations to be manufactured) allowing the operators to see what is going on on the floor, and where necessary, to allow the operator to make fine adjustments as required, right from the shop floor.
Semi-finished products and WIP is tracked without the need to create additional bills of materials. The system monitors the transfer of material to the production flow with withdrawal kanbans (expressed in storage or transport-handling unit sizes). WIP is adjusted with the value of the issued material.
The system then allocates the finished products to the correct transportation areas for delivery to the customer.
Share