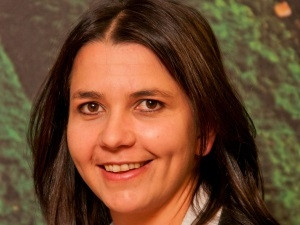
The disciplines of business continuity management are increasingly helping some of the world's leading manufacturers to identify and mitigate the complex set of risks they face.
"Manufacturers have to balance the need for long-term capital investment against the volatility of global consumer demand and agile competitors. Long supply chains and far-flung markets complicate the picture," says Karen Humphris, Business Continuity Management Advisor at ContinuitySA. "Many are finding that their business continuity management process has a big role to play, because it's just so good not only at identifying risks, but understanding the impact of each, thus making prioritising them much easier."
With the focus on long-term sustainability as a cornerstone of corporate governance, as articulated in codes like King III, boards of directors are increasingly concerned with ensuring companies understand all the risks they face, and have mitigation plans in place.
Business continuity management is a relatively new discipline that identifies risk and then quantifies its impact via a formal Business Impact Analysis. This process brings a certain rigour and objectivity to ranking how vital each element of the business is, and thus how much time, effort and money should be spent on mitigating its risks.
The risk profile of manufacturers, Humphris says, has been considerably worsened by the trend away from vertical integration, with greater reliance on an ecosystem of business partners to supply components or services "just in time". It's an approach that reduces capital tied up in inventory, but that makes the manufacturer vulnerable to problems at its suppliers.
Manufacturers can use three principles to help leverage the classic business continuity management process effectively, and make their businesses more resilient in general:
* Mitigate supplier risk. All suppliers are not equally important: if your stationery supplier runs into problems, it's a problem if you're a publishing company but not if you're a mining house. "You need to understand the impact that a failure by each one of your suppliers would have on your ability to achieve your strategy," says Humphris.
Once the key dependencies have been understood, risk mitigation is the next step. Some options would include building relationships with more than one supplier and analysing the logistics environment in order to predetermine alternative supply routes. Business interruption insurance is another possibility, but, says Humphris, manufacturers must never forget that reputational damage is not covered.
"I advise clients to build close relationships with suppliers and make sure they have their own business continuity programmes in place. This can be stipulated in service-level agreements," Humphris says. "It's also wise to have alternative suppliers identified and pre-qualified in case of the worst happening."
It also makes sense to hold buffer stocks of certain essential components, Humphris adds. Lean may be mean, but it's also risky; using the Business Impact Analysis wisely, it is possible to work out whether it's worth holding certain components , and how many.
* Mitigate equipment risk. Niche manufacturing operations aside, modern manufacturing is heavily dependent on equipment to achieve the quality and scale necessary. As the experience with key utility providers have shown, maintenance of essential components is something that cannot be ignored. Two mitigation options would be to enter into fixed maintenance contracts for essential equipment, and keeping decommissioned equipment in working order so that it can be brought back into service at need - rather as we see with mothballed power stations being put to good use now.
A lateral-thinking solution could be to enter into agreements with competitors, so in the event of a disaster, the other party would make at least some production capability available.
Reconsider your production strategy to minimise risk. It is preferable to have more than one manufacturing site so that, in the event of a disaster making one site unusable for a while, production can be shifted to the other site. Given transport costs and tolling, this type of decentralised approach is becoming more feasible, says Humphris. Another good strategy is to arrange for offsite storage of the finished product, something that has given many a company some vital breathing space when a production site suffers a disaster.
* Make sure your insurance is correct. It's important to connect the dots by making sure your insurance policy covers the risks you actually face, and that your premiums reflect the mitigation strategies you have put in place.
"Business continuity management is ongoing, so it will in time help make the manufacturer generally more resilient, and thus better equipped to cope with a market that seems likely to remain exceptionally tough," Humphris concludes.
Share