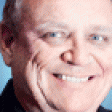
After the war, Japan changed manufacturing globally, and soon gave the US a "run for its money" in many industries. It reviewed the game and implemented a new philosophy based on the need to "eliminate waste" and a greater "respect for people". Many thoughts, ideas and articles have emerged over the years, with titles like "just-in-time", "lean manufacturing", and "theory of constraints" to define the new way of working.
The search for bottlenecks, the minimisation of stock levels, the shortening of set-up time, was on... the Kanban was invented.
The Kanban production control system is based on a needs/pull principle, which simply controls the manufacture of parts in a production line based on the requirements in the next step of the process. So, a work centre only starts the production of a number of units (say five) when it receives a Kanban (a physical card in a manual system). A work centre may receive Kanbans that requires the re-set-up of machines - so creativity, teamwork and practice is required to reduce the set-up times.
To get a feel of the Kanban system, first look at how it works manually. It is common that one workshop will produce parts faster than can be consumed by the next workshop in the line, so there will be a 'feed buffer' between them. As workshop B puts parts into the feed buffer, a withdrawal Kanban is set each time a new lot is added to show that parts are available for use. Each time the other workshop, workshop A, withdraws a lot from the feed buffer, the withdrawal Kanban is swapped for a production Kanban. The production Kanban is the trigger for workshop B to produce more parts.
Holistic view
Local efficiencies, the cause of massive stockpiles between work centres, are no longer measured - only the throughput of the entire organisation. As the system settles down, the 'pace' of the throughput will naturally be controlled by the bottleneck - and this is where an organisation should focus on efficiency and the investment in increased capacity. Feed buffers may still be designed into the system to minimise the effect of Murphy's Law - but the size of these can be carefully defined.
There is also a renewed focus on job creation within the space.
Top enterprise resource planning systems today have created electronic Kanbans that will allow the same control of the old card system, but do so using computers. Some systems will allow a mix of cards and electronic (some environments are not computer friendly), where the interaction between the cards and the computer are handled by a simple scanning of a bar code on the Kanban card. Microsoft Dynamics AX takes this even further, allowing the mixing of lean manufacturing (Kanban) techniques with its traditional Production Order (MRP II) production scheduling system. For example, a Kanban-produced component can be a sub-bill of materials (BOM) within a BOM.
For manufactures to be able to run their manufacturing using these lean techniques, they will need vendors of their raw products to also supply in a just-in-time manner. Systems today can be set up to receive formatted e-mail that will automatically create the Kanban/production order so the incoming orders can be processed in the order they are received.
Holding steady
There is also a renewed focus on job creation within the space, as manufacturers look to balance the integration of advanced equipment with specialised skills sets. It is widely acknowledged that equipment is being integrated to save on costs, to streamline operations and address the need to 'produce more with less'. It is an approach that is based on eliminating waste, of optimising resources and of creating growth - and the key thing behind lean manufacturing and a system like Kanban is that it can be applied in a broad sense, across most industries that rely on strategic manufacturing.
Improved output and job creation is inextricably linked to economic growth, so technology that facilitates this lean approach (to foster higher levels of productivity and more efficient operations) bodes well for a developing economy.
In South Africa, where manufacturing plays such a critical role in highly influential sectors like mining, infrastructure that empowers operators with an improved methodology to manage resources is invaluable.
So, is the country ready for lean manufacturing? Definitely! Manufacturers that are capable of short "jobbing" runs have emerged, and they are willing to go the extra mile to provide as needed and on time.
I will explore lean manufacturing further in subsequent Industry Insights, and delve into practical ways these proven principles may be brought into practice in the country.
Share