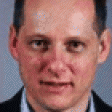
The manufacturing industry is set to be shaken by what some industry pundits call a 'fourth industrial revolution', following the steam engine, the conveyor belt, and early IT and automation technology. Like the three revolutions that preceded it, the fourth revolution, triggered by the Internet of things, promises to transform the way manufacturers operate and bring new levels of efficiency to industry.
Gartner defines the Internet of things as the network of physical objects that contain embedded technology to communicate and interact with their internal states or the external environment. The analyst group forecasts that there will be 30 billion such devices permanently connected to the Internet by 2020, and more than 200 billion intermittently connected devices by the same time.
The Internet of things sees the manufacturing industry move towards Internet-based systems and open protocols to reduce wastage and improve efficiencies. Using Ethernet and the Internet protocol, manufacturers are increasingly able to access and share data from all production systems in a common manner.
Intelligent networks
In the past, each fieldbus system - a system based on a family of industrial computer network protocols - needed a separate network and dedicated experts to operate it. By connecting machines, work pieces and systems to IP networks, manufacturers will (in theory) be able to create intelligent networks that allow for better visibility into - and higher levels of automation across - the value chain.
Improvements in safety, productivity and utilisation are the immediate benefits of the Internet of things for manufacturers.
Some examples of the benefits of this level of connectivity on the shop floor include enabling machines to predict failures and trigger maintenance processes automatically. In future, connected networks of equipment could evolve into self-organised logistics platforms that react to unexpected changes in production.
In the future, the Internet of things will see the floor worker in a manufacturing plant being moved further and further away from the assembly line or welding station and into an air-conditioned office, says Oracle SA middleware sales consultant Craig Nel.
"This shift is not just about the automation of manual tasks or processes, but also the intelligent integration of automated tasks and processes," says Nel. "Improvements in safety, productivity and [equipment] utilisation would be the immediate benefits, but the payback on investment could take a while to realise."
With access to sensor data from machines - production rates, temperature, oil usage and so on - manufacturers will be able to be more proactive when it comes to maintaining their equipment, says Geoffrey Francis, applications sales consultant at Oracle SA. The data could be linked to transactional data from the ERP system to provide insights that enable manufacturers to make better decisions. For example, if a manufacturer sees that the day shift is more productive than the night shift on the same assembly line, it could investigate whether more training of employees would help.
Share