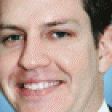
It is a good thing that green concerns are getting a high profile in the media, especially with climate changes. This is a broad trend in the office automation industry, as well as many others.
Along with the media attention, a much larger number of customers and equipment users have become aware of the environmental impacts of equipment usage and how they can minimise the negative aspects.
Realising that green practices can be cost-effective is a key element in the growing awareness seen in the market. Many companies are equally concerned that having green policies in place is a competitive advantage and a reduction of any possible reputational risk.
It is also a primary concern in this country that a company can realistically claim to be a good corporate citizen. But it also helps that there can be bottom line benefits from any green initiatives.
Typically, however, the green thinking in our industry doesn't go much beyond looking at power usage, the quantity of paper used and maybe also the recycling of components and/or packaging.
While these are all important factors to take into consideration, there are others that should be looked at simultaneously.
Star performers
If we compare two of the major international standards, it illustrates how there is a more holistic view developing of what is really involved in effective initiatives to achieve a better environmental impact.
Most people are quite familiar with the Energy Star awards seen today on a wide range of equipment and appliances - even on buildings overseas. The Energy Star certification was started by the US Environmental Protection Agency in 1992 and was subsequently supported by other countries - including the European Union - as a voluntary programme to increase energy efficiency and reduce power consumption. The basic idea is to reduce power usage and therefore reduce greenhouse gas emissions from electricity generation.
While that is a good idea, Energy Star doesn't look at aspects of equipment or systems beyond the power efficiency. In the EU, a further standard - TCO (Tj"anstem"annens Centralorganisation) Certification, a Swedish organisation (that has nothing to do with the total cost of ownership acronym), has been in use for quite a while and this takes into account energy use, ergonomics and ecological impacts of hazardous substances.
One of the standards that is less well-known, but which has an even longer history, is the German Blue Angel certification. This goes back to beginnings in 1978 but it has developed over the years into one of the most demanding standards anywhere in the world. It is also frequently revised, which keeps pressure on manufacturers to improve their products. If a device achieves certification this year, it might not make the grade a year later.
Two of the key requirements for Blue Angel certification are low energy usage and the use of recyclable materials.
Beyond this, there are high standards for the elimination of hazardous substances in devices manufactured and equally high restrictions on substances emitted during operation - and even noise pollution standards.
Health issues
International standards bodies and, consequently, manufacturers are looking at improving device performance in a wide range of green areas.
Michael Powell is product marketing manager at Kyocera Mita South Africa
This might seem like it's going almost too far but anyone who has walked into a closed office space where there are many printers will know that the "air pollution" is quite noticeable.
These printer emissions include various volatile organic compounds, ozone and simple dust (particle emissions from the mechanical components and toner). None of these are healthy for people to be exposed to in significant quantities or for prolonged periods of time.
You might be able to live with a noisy printer and suffer no more permanent harm than ongoing annoyance, but prolonged exposure to high levels of air pollutants will really affect your health.
The Blue Angel standards are more stringent than any others and look at keeping emissions to well below the safety levels set by industrial safety regulations.
Along with the equally high requirements that this certification has for power usage and use of recyclable materials and longevity of components, it is assured that a device that achieves Blue Angel awards meets the best worldwide standards for being environmentally friendly.
The point of all this is that international standards bodies and, consequently, manufacturers are looking at improving device performance in a wide range of green areas. This goes way beyond the original concerns about electricity usage or what kind of paper is being used.
The drive to achieve environmentally friendly technologies and ways of working is not a simple matter. It is multifaceted and it requires a very holistic approach from buyers and sellers of all types of equipment to make sure green objectives are effectively met.
Fortunately, we see more and more people throughout the industry who are committed to making real progress in these areas.
* Michael Powell is product marketing manager at Kyocera Mita South Africa.
Share