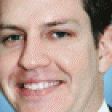
Most equipment manufacturers offer solutions for printing and imaging, and there are plenty of third-party solutions that can also be considered.
These are not just “nice to have” or optional extras. If such solutions are used correctly, they can offer significant savings on operational expenses, as well as increasing efficiency and productivity for all the business processes where office equipment is a key element.
I am not talking about a “paperless” office. Documents in hard copy are still a common need for most companies, whether because of ingrained traditions or practical necessity.
What I am saying is that full use of what equipment can do will make operations cheaper and easier.
Policy in position
The first step is to make sure there is a policy in place that governs printing, imaging and faxing. The vast majority of companies are now working with MFPs, which do all these things. Even if there are separate devices for the different functions, it still has to be managed and controlled.
A modern colour copier can produce tens of prints every minute, each costing as much as a rand per page. So it can be seen why this process needs to be well managed. Modern equipment typically has the ability to assign job codes, and these can be used to block or limit colour printing.
Another example would be the use of double-sided printing. It is seldom necessary to print single-sided and the savings here can halve the costs. There might be a cost involved in making duplex printing the default setting, but this is rapidly paid for by the savings achieved.
As a last example, I can highlight the traditional preference for using faxes. It is still prevalent that users will print a document and fax it, when it is quicker - and much less expensive - to scan and e-mail it.
All these functions can be controlled by settings on the equipment and/or administrator settings that can be enforced on a managed network of devices. It is important that users know whatever policy is put in place so that they have awareness of these issues, but it can be effectively implemented using the abilities that most equipment already has built in.
Get the picture?
Imaging is another trend that companies don't always take full advantage of. Working with soft copy or electronic documents is much easier and faster than working with hard copies that have to be stored and are difficult to search. There might be specific reasons to work with paper documents, but the majority can be handled electronically just as well - and with greater convenience, efficiency and cost savings.
When documents are scanned, they automatically become available for other IT network services, especially whatever document management solution the customer has in place or deploys.
It is still prevalent that users will print a document and fax it, when it is quicker - and much less expensive - to scan and e-mail it.
Michael Powell is product marketing manager of Kyocera Mita South Africa.
This opens up possibilities for document routing. This is the most basic level of workflow solution. A full workflow solution is a complete model of the steps involved in a business process. Document routing is just automating the distribution of documents according to company rules and procedures. Automating this process has a big impact on productivity, quite apart from making sure that communications are facilitated and procedures adhered to.
Document routing doesn't change an existing process that might be working well for a company. It does make the process faster and safer.
Automated document capture is another feature that people don't use extensively, although it has many advantages. This will produce a PDF, which is bar coded so that the information in the document fields is built into the document. This can be scanned, faxed and read by another device so that there is no need for manual entry of data - eliminating the possibility of errors.
Lastly, a number of output monitoring solutions can be used - from equipment manufacturers or third-party vendors - which can be deployed to measure the real costs, on a per-job basis. This means a company can audit whether policies are being applied and how effective they are, as well as the individual costs of copying, printing or faxing involved in specific projects.
Overall, I am focusing on the optimisation of processes by using the features that an office's equipment already has. There are significant savings that can be achieved.
There are three steps to making this happen: have a clear policy in place that governs how the equipment can be used; configure settings on the machines and through the management solution to make sure the policy is enforced; and monitor the results at the output end.
Doing this, using the features the equipment often has built-in, leads to savings in costs on the equipment itself and for all the business processes that depend on the use of the office equipment.
* Michael Powell is product marketing manager of Kyocera Mita South Africa.
Share