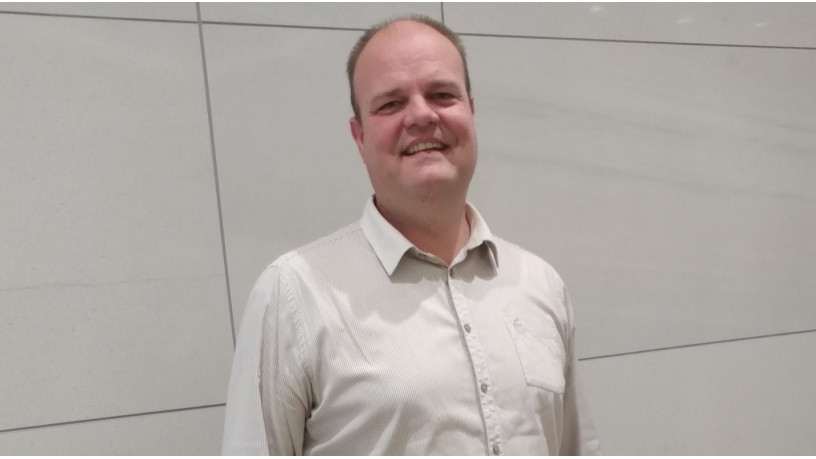
In manufacturing, accurate and comprehensive real-time information about plant floor operations is essential to making informed decisions that drive productivity. What could be more crucial than the equipment itself? Downtime, which is detrimental to any business, is especially damaging and costly for manufacturers. According to Mining Global, each hydraulic power and belt drive failure can result in up to $180 000 in lost production.
Yet many organisations lack the insight and visibility they need to refine their operations in a cost-effective and proactive way. In Africa in particular, asset managers are under severe pressure to keep their equipment performing, despite constrained budgets and aging infrastructure. Advanced enterprise asset management (EAM) solutions give companies deep visibility into their assets and allow them to plan and prioritise maintenance activities more effectively. This, in turn, curbs the tendency to overspend or underspend on maintenance practices.
According to Barry Diedericks, EAM Subject Matter Expert at Softworx, Infor's Master Partner in Africa, there are five distinct ways in which effective EAM improves plant floor productivity. "Firstly, the right EAM solution will reduce movement to optimise task efficiency. It will also improve supply chain scheduling to reduce bottlenecks and increase equipment reliability. By optimising inventory levels, shortages are reduced. Lastly, automated data collection automates processes, which speeds up plant floor operations."
"Movement" is considered one of the seven wastes of lean manufacturing. According to Paul A Myerson, Professor of Practice in Supply Chain Management at Lehigh University, waste of movement "occurs when temporarily locating, filing, stocking, stacking, or moving materials, people, tools, or information." Effective EAM decreases the time and labour needed to complete tasks by reducing movement, which in turn decreases the risk of damage, or the loss of parts and tools.
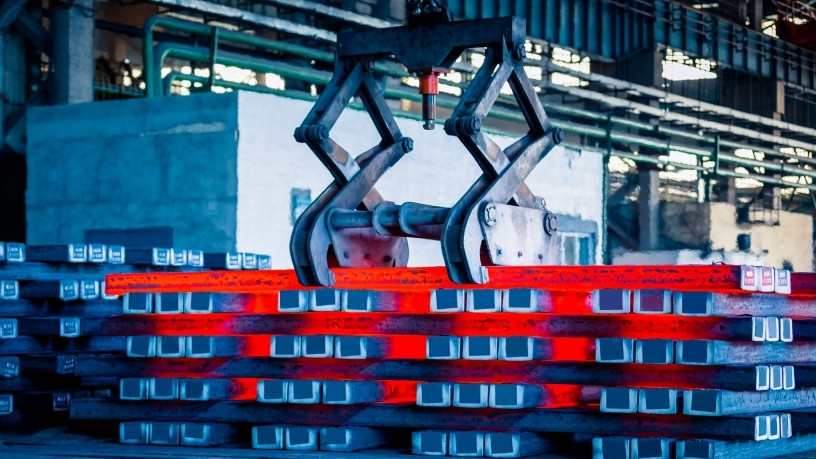
In any manufacturing organisation, it is clear that things do not always go according to plan. "Production flow can be greatly impacted by the availability of material or by disruptions," adds Diedericks. "With early detection capabilities and real-time access to capacity, availability, qualifications, and interdependencies of employees, equipment, tools, and materials data, however, you have access to the information you need to adjust schedules to accommodate those disruptions." This information lends itself to efficient supply chain scheduling, minimising delays and down time.
Properly maintained equipment reduces plant floor operational risks, preventing unplanned equipment downtime. Poorly maintained equipment adversely affects the quality of products being manufactured, which in turn reduces plant floor productivity even further by creating additional rework hours. "This is a problem that is easily avoided through innovative EAM," he adds. "It is effective in decreasing the likelihood of unplanned downtime. Through a strategic approach to asset management, equipment performance data can be analysed for key trends and anomalies, empowering the organisation to act proactively rather than reactively."
A key element of plant floor productivity is the material required to manufacture the product. If this material is not available, production grinds to a halt. However, when manufacturers suffer from inventory shortages the proper response is not to increase safety stock levels. Not only does this reduce cash flow and increase inventory carrying costs, but research has shown that increasing safety stock levels isn't even a sure guarantee against inventory shortages. Diedericks believes the best approach is to ensure accurate and timely visibility into your inventory is at hand. "This allows you to know exactly what components are running low in stock, detect potential issues, and rectify them before they become real problems."
Automating your plant floor processes with automated data collection tools, like barcoding, drastically speeds up inventory and asset data collection and analysis, while improving data accuracy. "With barcoding, key inventory and asset data (such as quantity and location) is automatically captured. This ensures slow and error-prone manual data entry is bypassed. Barcoding technologies, such as RFID, also reduce equipment downtime. This allows manufacturers to identify usage patterns and reduce costs by implementing a need-based (rather than an arbitrary calendar-based) maintenance schedule."
With complete visibility into plant-floor operations, manufacturers are afforded access to the information needed to make the most effective use of constrained resources. This illuminates areas where throughput and efficiency can be increased, while promoting better material and asset management. Being able to see how all of the pieces fit together - in real time - ultimately ensures more efficient operations and better decisions.
"By recognising priorities, increasing asset visibility, accurately analysing patterns, and responding with greater agility, companies equipped with EAM solutions can reduce costs even as they reduce risk," concludes Diedericks. "They can also perform at higher levels of reliability, quality, and safety without needing more resources."
Share