Panasonic Business Systems PE and Powell Tronics have implemented an asset management system that makes use of active RFID tags for Tavcor Volkswagen, a motor vehicle dealership based in Port Elizabeth, South Africa.
Martin Taverner from Tavcor says the focus of the After Sales Division is on customer satisfaction via efficient service of vehicles. The company has expanded its premises and found the need to be able to locate and monitor all vehicles booked in for a service. The reason for this is to provide a fast and efficient service time to the customer and to ensure no loss of keys or vehicle theft from the premises.
Before the asset identification management solution was implemented, it took service advisors too long to trace a vehicle on the premises due to the size of the building, and with an excess of 60 vehicles being booked in per day. Besides the vehicle being tagged, the keys are tagged as well.
The system installed also provides the dealership with the ability to track the service or repair progress of a vehicle on the premises and audit Tavcor Assets. This was a manual process before and the benefits of being able to locate vehicles and keys in real time are extensive to Tavcor.
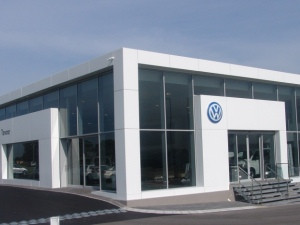
Powell Tronics, as a solution provider, had customised the Asset Identification Management system for Tavcor, as it did not include a vehicle identification process before, but only an ICT asset management module.
The customisation included a vehicle tracking system, a key tracking system, a job progress 'live updates' grid and a reporting system. It would provide the dealership with live updates on the location of all vehicles and keys on premises every 1.2 seconds, and enable service advisors to locate vehicles and accurately estimate completion time for customers. It would also allow the vehicles to be parked, ready for collection, in the handover area, and the keys to be located quickly.
To start the installation process, wireless zones were created throughout the service-related areas with an antenna to determine the range in each area. From there, the system tracks the location and progress of the vehicle throughout the day. This process allows the dealer principal, service advisor, quality controller and service manager to track the progress of a vehicle's service, and monitor for potential carry-over and problem vehicles. The service advisor will now be able to print out a movement and works report that is most importantly time stamped as an audit trail for each vehicle. Each individual who has access to the software will log in with their unique username and password via a Web interface. This is set up by an administrator upon implementation.
"Each area is listed in the grid, and if a vehicle has a problem in a specific area, a user can add a note, such as 'awaiting parts'. All vehicles' booking history remains on the system, and once booked in, will be allocated an available RFID tag, as they are re-usable on a daily basis.
Having implemented the solution and achieved all its requirements at the PE pilot site, Tavcor plans to roll out the solution to its branches nationally as well as add its ICT assets for inventory purposes in the future.
Asset management system
* 300 active RFID tags
* 23 zone readers including antennas in seven areas
Share