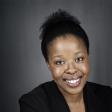
The Department of Science and Innovation (DSI) has officially unveiled a R97 million 3D printing project to improve access to medical devices for people living with disabilities.
The DSI launched the project − called the Medical Device Additive Manufacturing Technology Demonstrator (MedAdd) − in partnership with Central University of Technology (CUT), as well as its Technology Innovation Agency (TIA).
3D printing, also known as additive manufacturing, is a technique that uses a device to create physical objects from digital models.The range of 3D-printable materials has grown significantly over the years, making the technology appealing to a wider array of industries.
In 2019, the 3D Printing in the Medical and Dental Industry 2019-2029 report identified 3D printing tech as key to the development of the medical industry.
The DSI’s 3D printing initiative has been established in response to local industry challenges, with the aim to bridge the innovation gap in the use of additive manufacturing for medical devices.
Speaking during the hybrid launch of the project, MC Dr Vuyisile Phehane, executive: bio-economy at TIA, indicated the Free State’s CUT is the leading South African university in the application of additive manufacturing for the production of customised medical implants.
However, the impact of this expertise and resources on the development of a medical device manufacturing industry has been limited, mainly due to a lack of equipment specifically for medical device manufacturing, Phehane continued.
“The medical device additive manufacturing tech demonstrator project is located at the university’s Centre for Rapid Prototyping and Manufacturing (CRPM).”
Healthy collaboration
The CUT’s Centre for Rapid Prototyping and Manufacturing has been doing work over the years in the design, development and manufacturing of medical devices.
According to the DSI, MedAdd functions under the CRPM's ISO 13485 certification, which acts as a safety net for small companies seeking to develop and industrialise new products, de-risking their innovative development before fully-fledged commercialisation.
Dr Rebecca Maserumule, acting deputy director-general for technology innovation at the DSI, said the advent of the COVID-19 pandemic highlighted the importance of African countries proactively investing in medical research and health innovation.
As a result, health innovation is one of the areas the DSI identified for the purpose of enhancing the impact of science in society.
“Our overall objective in this space is to help grow the health economy by providing locally-developed and relevant diagnostics and medical devices with a view to boosting their manufacturing,” noted Maserumule.
“More specifically, we seek to enhance our existing capacity to manufacture active pharmaceutical ingredients, vaccines, biopharmaceuticals, diagnostics and medical devices to address the disease burden, while ensuring the security and sustainable supply of essential therapeutics and prophylactics.”
CUT Council chairperson Matthew Rantso added that since 2015, more than 1 000 patients had been assisted through the support of state and private hospitals, the expertise of the CRPM, and funding from the DSI, TIA and other strategic partners.
Rantso pointed out the MedAdd project had brought the CRPM and industry together in planning and investing resources in a collaborative manner, which is a big plus for the university. From a product development point of view, he added, this was an opportunity for CUT, business and industry, through government, to create African solutions for South African challenges.
“We look at the success of MedAdd as just the beginning towards the next stage of technological innovations that will be followed by many other landmark projects like this one.”
3D printing in action
South Africa has, in recent years, made significant inroads in 3D printing, with many local use-cases and designs being developed for the medical industry.
In 2020, engineers at the University of Johannesburg (UJ) designed and developed portable 3D-printed mechanical ventilators, in an effort to step up the fight against COVID-19. The portable UJ ventilator allowed off-grid operations for up to one-and-a-half hours.
Earlier that year, the higher learning institution created open source, cheap ventilators to help fight the pandemic.
UJ’s Library Makerspace division developed 3D-printed surgical face shields, in an effort to meet the rapidly-growing need for personal protective equipment for healthcare workers at the height of the pandemic.
As part of the 2019 Women’s Monthactivities, the Council for Scientific and Industrial Research (CSIR) showcased some of the breakthroughs made by its female researchers, using the world’s largest 3D printer, which is housed at the CSIR.
The 3D printer uses a powder bed fusion process called selective laser melting, where a 5kW laser melts titanium powder. A bed of powder is added for each layer and the subsequent layers are fused through the selective laser melting.
Share